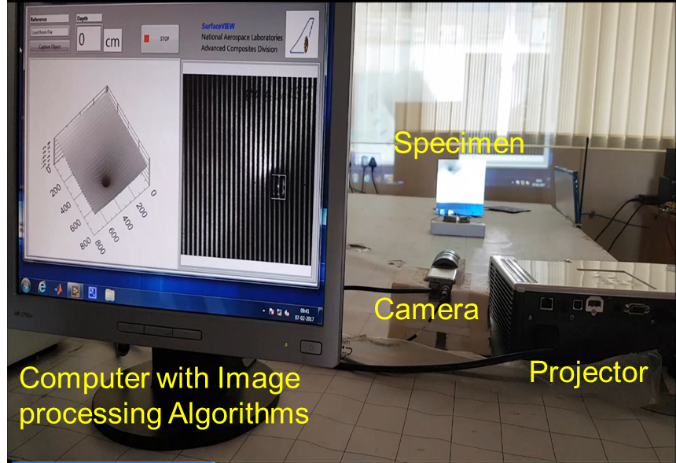
Surface Damage Detection using Image Processing
One of the widely used inspection methods to ensure structural integrity of an aircraft is the visual inspection. In this technique a qualified inspector goes around the aircraft and looks for surface damages like cracks, dents and corrosion. The manual inspection is generally time consuming and ineffective due to inspector fatigue or boredom. This could lead to missing of some damages by the inspector. The unavailability of standard recording procedures for manual inspection for future reference is a major concern. This raises the need for an automated inspection system that carries out a faster, efficient and reliable inspection with archival of inspected data. As surface damages manifest as deformations/dents/aberrations on the surface, 3D reconstruction of surface using image processing can provide more insight into surface damages.
Specifications
NI PXIe 1082Q with Controller, NI PXIE 8840,NI 8234Dual GB Ethernet frame grabber card and Basler pilot, colour, pia2400-17ge camera
Major milestones / results of this technique
SHM group is actively working on developing a methodology using 3D vision/ image processing based surface damage detection. Technique based on fringe profilometry is being developed in the lab, where images of the structure under inspection with fringe patterns is projected is captured using cameras, and analyzed with image processing techniques to construct the surface profile. Algorithms are developed to identify the damage location with size and is demonstrated on laminate level.
|
|
Fringe profilometry set up |