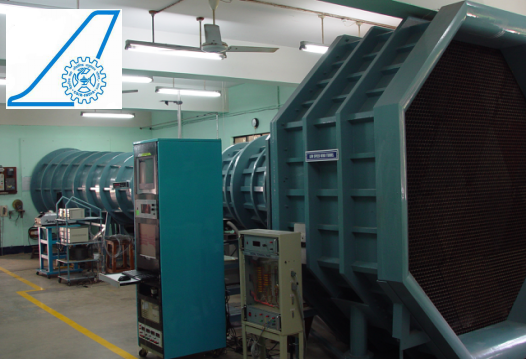
0.55 Low speed wind tunnel
The 0.55m Low Speed Wind Tunnel was commissioned in 1970 with a circular cross section test section. The circular test cross section was converted into a square cross section in the year 2000. The unique feature of this facility is that it can go as minimum of 0.5m/s. This tunnel is an open circuit type wind tunnel with a contraction ratio of 16:1. This tunnel is majorly used for research applications both basic and applied in nature.
Test Section size and shape |
0.55m x 0.55m x 1.90 m Square cross section |
Speed range / Mach number range |
Velocity range 0.5m/s to 40m/s |
Reynolds number range (per m) |
0.03 x 106 to 3 x 106 |
Freestream turbulence level |
< 0.2 % |
Pressure fluctuation level |
Cp variation < 0.05 |
Type of tests performed:
- Steady and Unsteady force & moment measurements (T5)
- Steady and Unsteady pressure measurements (T4)
- Wind engineering – Cup Anemometer calibration
- Flow visualization: Tuft, Surface and Smoke Flow visualization (T7-T9)
- Non-intrusive flow diagnostic tests: Particle Image Velocimetry (PIV) (T2), Hot wire anemometry (T10), Hot films (T12) and Laser Doppler Velocimetry (LDV) (T13)
- Special tests (other than those listed above)
Test control parameters:
- Sting mounted support: Pitch -10° to 30° Steps of 0.1°
- Typical test duration: Continuous, up to 4hrs
- Stagnation pressure & Temperature range: Atmospheric pressure and temperature
Instrumentation:
- Pressure Measurements: Furnace manometer, Setra low pressure transducers and ESP scanner
- Velocity Measurements: Particle Image Velocimetry (PIV), Hot wire anemometry, Hot films and Laser Doppler Velocimetry (LDV).
Data Acquisition Systems used:
PXI -1033 integrated controller PXI chassis consist of
1) PXI-6281 DAQ card (18 Bits resolution with 625KS/s M series card) connected to SCXI-1000 chassis with 1520 signal conditioning Module.
2) PXI-6533 High speed switching DIO card.
Special test rigs and test techniques developed:
Scotch yoke mechanism for precise control of the oscillating frequency and amplitude used for oscillating airfoil experiments.
Major Customers:
AR&DB, NAL’s Centre for Societal Missions and Special Technologies, ADA, Mahindra and Mahindra
Milestones achieved:
- Flow control strategy for low speed cavity aerodynamics
- Studies on leading edge tubercled airfoils
- Studies on drag reduction for bluff bodies using forward splitter plates
- Flow control over an NACA 4415 airfoil using synthetic jet actuator
- Studies of low Reynolds number on an Eppler 61 airfoil with and without Gurney flap
- Study of dynamic stall on an oscillating airfoil
- Studies on powered Black kite and Golden Hawk MAV’s
- Calibration of Cup anemometers for NAL’s weather monitoring stations of Centre for Societal Missions and Special Technologies